ENERGY SAVINGS : STEP-BY-STEP PROCEDURE
“The only Zero-Carbon energy is the energy that we do not use”. It is obvious that any decarbonization program should start with identifying energy conservation actions and implementing them.
Energy saving actions depend to large extent on the nature of activities. Companies have very diverse processes which consume energy, which makes it difficult to elaborate a “one-size-fits-all” playbook. But generally, the following methodology can be followed:
- Make an inventory of energy usages on the site, which yields:
- Global site energy balance
- Profiles and history of the uses of energy and production;
- Energy breakdown by energy source and for process/area/utility
- Calculation of Key Performance Indicators (KPIs)
- Impacts of important parameters (operating parameter, weather…)
- Determine an Energy Baseline (Reference consumption)
- Carry out an Energy Audit/Workshop to determine potential energy savings actions
- Estimate implementation costs or submit different projects for quotation
- Sort out the different projects depending on Return On Investment (ROI), available resources and investment
- Implement projects
- Monitor and measure progress accomplished
Ideally, a measurement plan has been implemented and energies are measured and can be monitored during those phases. However, if no data is available, energy breakdowns can still be estimated from equipment nameplate data and observations or reporting from site operating staff. The resulting estimated overall consumption should nevertheless be reconciliated with energy bills.
The following figure shows a typical energy breakdown for an industrial site.
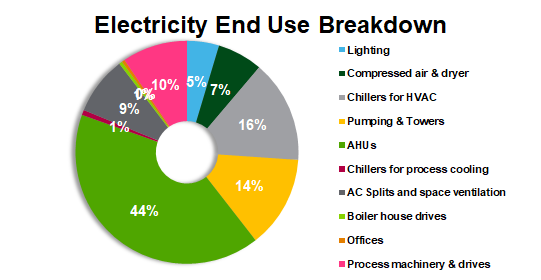
This breakdown shows the areas where to focus attention. In this case, the Air Handling Units should be the first subject of attention. Clearly, the fans, which ensures the air circulation in the different process areas, consume a substantial part of the overall site electricity. Therefore, the air flow rates in the numerous Air Handling Units should be examined.
Then the chillers and the pumping system consume each about 15% of the total. This figure clearly shows that this site’s electricity is mainly devoted to maintaining climatic conditions, because the sum of AHU, Pumping and Chillers make up 74% of the total.
IDENTIFYING ENERGY SAVINGS ACTIONS USING THE 3C METHOD
The “3C” method enables the identification of energy savings actions in a wide variety of situations. It is based on common sense, but requires the involvement of the site staff – it should be applied to all energy consuming zones (utilities as well as manufacturing processes). It enables non-experts to carry out a preliminary screening of energy conservation measures or alternative ways for the process steps or the Utilities.

This method should be applied in the order shown in the figure. Three questions should be asked while examining any process that consumes energy. Cancel ? Cut down ? Change ?
CANCEL
Can you cancel the need for energy? In many instances, some processes can simply be turned off. In industrial sites, a myriad of equipment stays powered even when not in use.
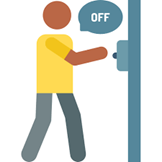
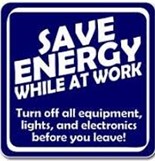
Sign postings to increase staff awareness
Most fume extractors remain powered all the time, even if the plant is closed. In everyday situations, the same applies in many cases. For example, people should be instructed to turn off the light when it is not needed, turn off their computer and printer when they leave work; municipalities should make sure that lighting is off during the daytime etc. Home equipment (video, TV, etc.) stays idle during most of the time – and consumes power. Hence, the “turn-off equipment when not in use” option represent an immense potential for energy savings – and therefore for decarbonization.
Equipment shut-down can be automatized by slaving switches to an equipment mains supply, or by other means (e.g., electromagnetic valves ahead of machines). Car rides can simply be cancelled if the distance is very short. Whenever a process does not consume energy or material, it does not emit GHGs.
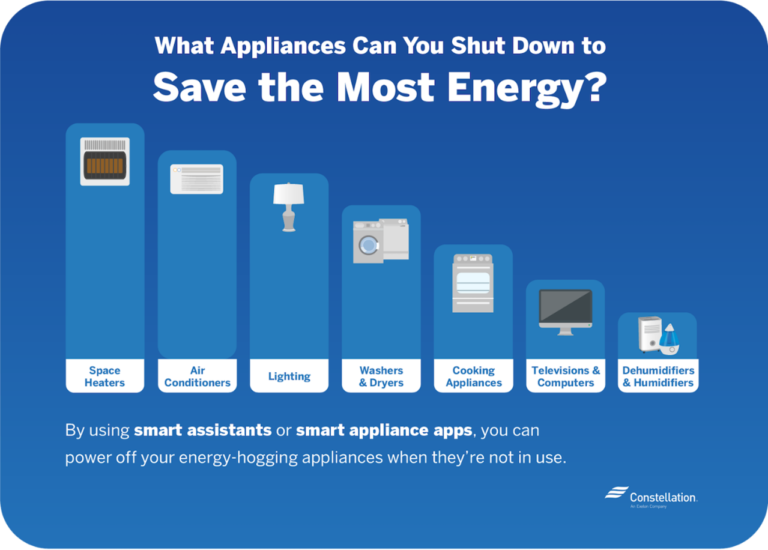
In an industrial site, this means setting up an Energy Savings Plan. A thorough examination of the all the consuming processes enables the identification of energy savings actions. High-efficiency equipment can also contribute to energy consumption reduction, while providing equal or even better service. The applications cover items such as preventive maintenance of equipment, thermal insulation for equipment or buildings, super-efficient electric motors, sophisticated controls, close monitoring, timers, presence detectors for lighting, intelligent LED lighting, etc.
Can you reduce energy consumption?
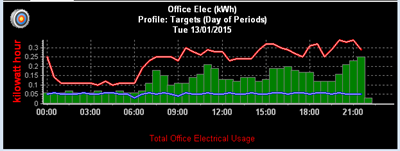
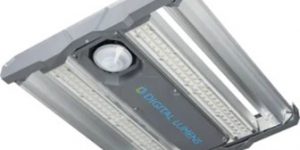
Can you change the means that you need?
by switching to different means energy consumption can be drastically reduced, sometimes even to zero.
Examples could be: using freecooling to cool water instead of using chillers, substitution of compressed air tools by electric tools; replacing venturis by vacuum pumps; etc.
Changing the means could also include using a different process for production. In this context, electrification will certainly be the most powerful tool – provided electricity is provided by low-carbon emitters.
Examples of questions to brainstorm:
– Cancel the need for energy? “Do we really need to air-condition this area? “,” Do we need to use 8°C water to cool down an oven that is at 700°C? “
– Cut-down the need? can we operate the air compressor at 7 barg instead of 8 barg? Can this oven be cooled with water at 15 ° C or water at 45 ° C? Can we air-condition with water at 10°C instead of 7°C?
– Change the need? Can we use an alternative method? Can I use an air fan for cooling, instead of compressed air? Can I use free cooling to cool this oven? Can I replace the air venturi by compressed air ?
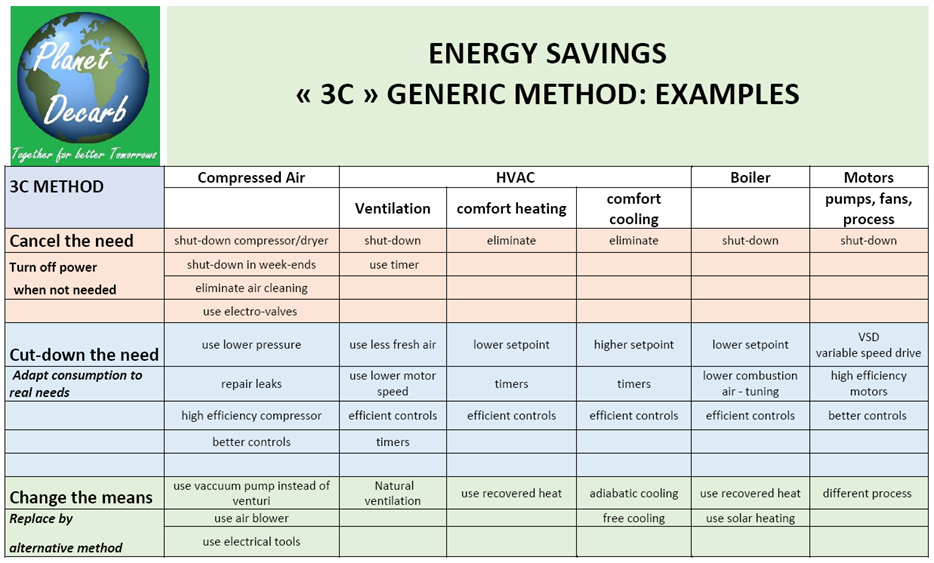