Cement plays a major role in building economic development of countries, its industry is a prime sector for the building materials and civil engineering industries.
Cement is a rocky powder that can be shaped into any desired form when mixed with water and it hardens into a rock-like consistency once dry. It can be used alone but usually it is employed in mortar or in concrete. Mortar is a mixture of cement and sand that serves to join bricks and blocks together, and concrete is a mixture of crushed rock, sand, and cement that is used to construct buildings, bridges, roads, pipes, dams, and other structures. (Source: encyclopedia.com, britanica.com)
The following figure gives main differences between cement, concreate and mortar.
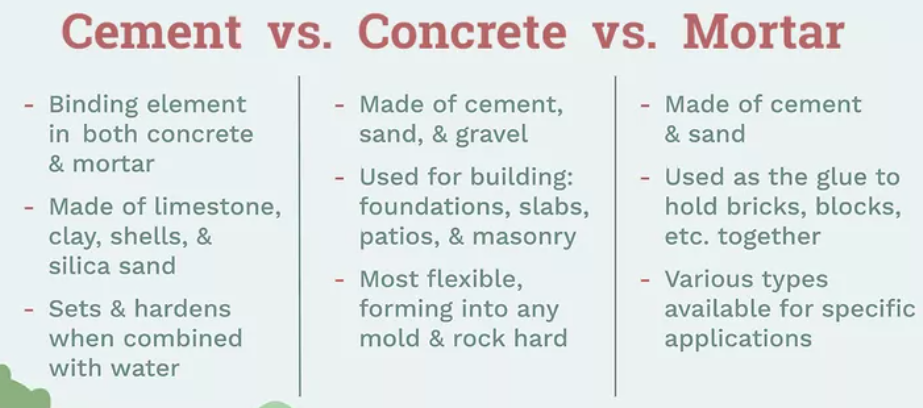
Cement classification
Depending on how it reacts with water, cement is classified in the two following categories:
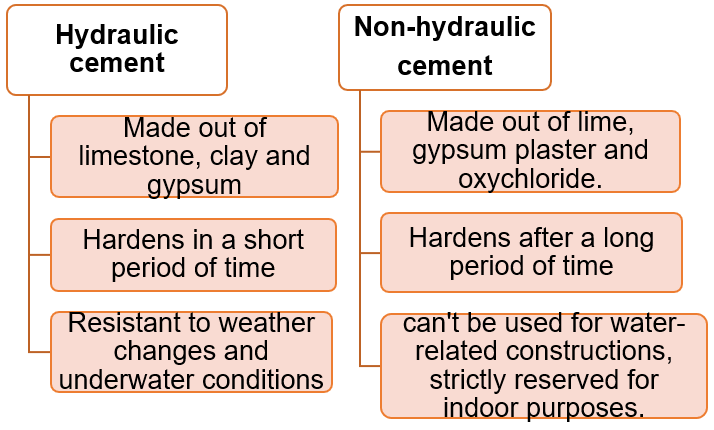
Types of cement
There are various types of cement in the market today, varying in properties, use and composition. Some of these types are given in the table below. (Source: cementconcrete.org, hanson.ny, stylesatlife.com)
Cement type | Description |
Ordinary Portland cement | OPC is the most common type of cement used in general construction purposes (concrete, mortar and plaster) where there is no exposure to sulphates in the soil or in groundwater. |
Portland pozzolana cement | PPC has a high resistance to different chemical assaults on concrete. It is widely used in construction such as waterfront structure, marine structure, dams, bridge piers, thick foundation where mass concrete is used and in sanitation system like Sewers. |
Rapid hardening Portland cement | It is more finely ground than OPC. Its 24 hours strength is almost equal to that attained by OPC after 3 days. Its use allows early removal of shuttering and thus saves time and money. It is generally used in road work and bridge construction where the time factor is very important. |
Extra rapid hardening cement | It gains strength rapidly and is obtained by adding calcium chloride to rapid hardening cement. It is widely used in cold weather concreting, to set the cement fast. |
Portland slag cement | It can be used for all purposes for which OPC is used, mainly in precast and ready-made concretes and building structures that require high-temperature resistance |
Hydrophobic cement | It contains water-repelling properties to avoid cement loss in areas affected with frequent water contact. It is convenient for storage during longer periods in extremely wet climatic conditions and is used in dams and underwater constructions. |
Low Heat Cement | Special type of cement that releases low heat of hydration. It is used in mass concrete construction like gravity dams, it is less reactive and the initial setting time is greater than OPC. |
Quick Setting Cement | It is used for constructions that need rapid setting, such as underwater structures and in cold and rainy weather conditions. |
Sulphate Resisting Cement | It is manufactured to resist sulfate attack in concrete, it can be used in water storage sumps and drainage work. |
High alumina cement | Referred to as Calcium Aluminate cement or Aluminous Cement, it has a high compressive strength, it is fire-resistant and it is used in constructions that are subject to high temperatures like a workshop, refractory, and foundries. |
White cement | It is manufactured using raw materials that are free from iron and oxide, it leaves a smooth finish on the surface and thus is used as a leveller product |
Air Entraining Cement: | It is used for increasing the cold resistance in concrete, especially when it is subjected to frequent freezing and thawing |
Cement production
The following figure gives worldwide cement production by country.
Highest cement production worldwide was held by China in all years given in the figure. It’s production in 2020 was estimated 2.2 billion metric tons, a value that is less than 2019’s 2.3 billion metric tons.
According it IEA, China accounts for about 55% of global production, followed by India at 8%. (Source: iea.org)
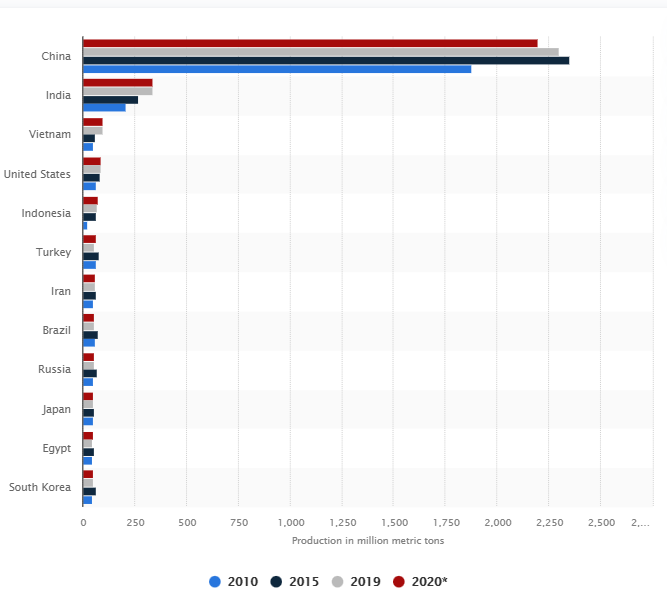
Cement industry emissions
Cement industry is one of the largest emitters of anthropogenic carbon dioxide, nitrogen and dust in the atmosphere.
The following figure gives worldwide cement manufacturing carbon dioxide emissions in million metric tons by country.
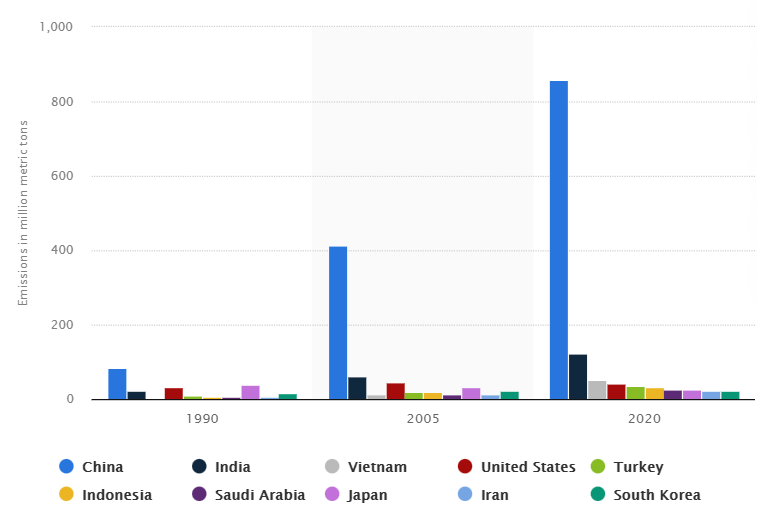
Emissions from cement manufacturing differ in each step of the process. We can distinguish three parts of the process that generate emissions:
- Calcination: The main constituents of cement (limestone, clay, and chalk) are calcined.
Limestone is a rock composed of calcium carbonate (CaCO3), when calcined CaCO3 breaks into CaO and CO2 that is released to the atmosphere.
Clinker releases about 1.1 lb (0.5 kg) of carbon dioxide for each 2.2 lb (1 kg) calcined. - Fuel: Heat necessary for calcination is provided through fuel burning. The amount of CO2 released depends on the type of fuel used; coal, natural gas, fuel oil, and other fuels are used for this purpose with coal being the most common.
- Electricity: Electricity is used to run the machines that crush and grind limestone before and after calcination and to run other manufacturing means.(Source: encyclopidia.com)
The following figure gives global cement industry emissions in 2019 detailing the share of each step of the process.
Global cement industry emitted around 2.3 gigaton of CO2 (Gt CO2) emissions in 2019. Out of the 2.3 gigatons of CO2 generated, 1.4 Gt CO2 is related to the process-related emissions (chemical reaction during the calcination process), 0.6 Gt CO2 is related to fuel use (also called Direct emissions) and 0.3 Gt CO2 from electricity use (also called Indirect emissions).
Energy-related emissions from fuel and electricity use account for only 40% of total GHG emissions of the global cement industry and the remaining 60% is related to the process emissions from calcination.
(Source: globalefficiencyintel.com)
Depending on total cement industry emissions given above and the global GHG emissions of 52 Gt CO2-e in 2019 (includes non-CO2 GHG emissions as well) reported in UN Emissions Gap Report 2020, the global cement industry is responsible for around 4.5% of total global GHG emissions.
Depending on the total cement industry emissions given above and the global CO2 emissions of 33 Gt CO2 in 2019 reported by IEA, the global cement industry is responsible for around 7% of total global CO2 emissions.
(Source: globalefficiencyintel.com)
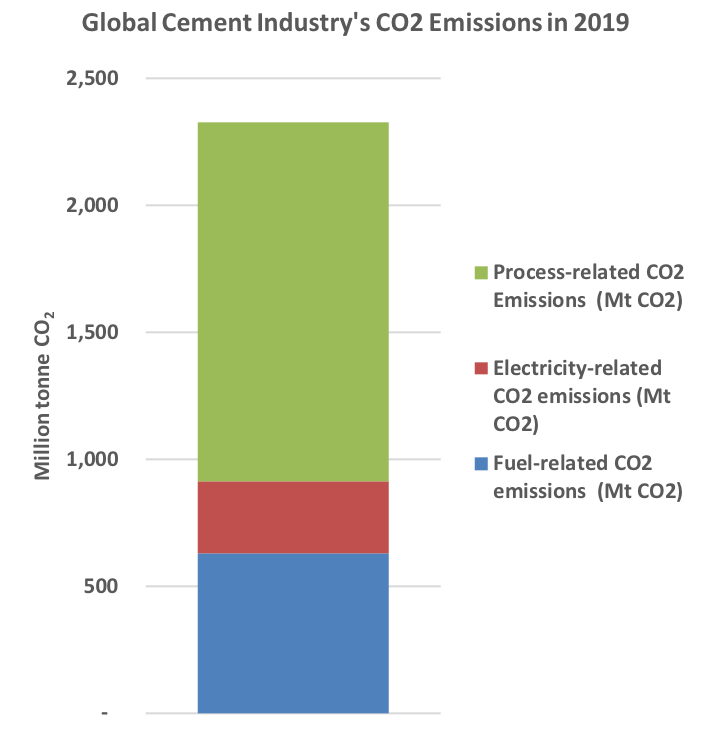
Cement industry data
According to the Global Cement and Concrete Products Market Report (2021 to2030), the global cement and concrete products market is expected to grow from $333. 26 billion in 2020 to $365. 58 billion in 2021 at a compound annual growth rate (CAGR) of 9. 7%. The growth is mainly due to the companies rearranging their operations and recovering from the COVID-19 impact. (Source: pmewswire.com)
According to IEA, direct CO2 intensity of cement production increased 1.8% per year during 2015-2020. In contrast, 3% annual declines to 2030 are necessary to get on track with the Net Zero Emissions by 2050 Scenario. (Source: iea.org)
According to Kyrros data for European cement production review 2020, UK and Spain experienced a decline in cement plant activity exceeding 15%, with France falling slightly below 10%, Italy maintained a relatively stable cement plant activity curve according to the sample, as well as Germany. This is shown in the following figure.
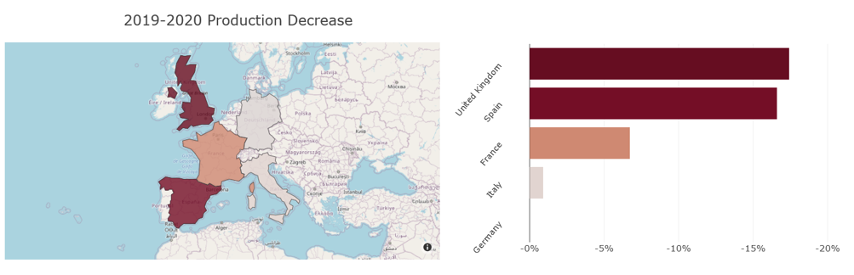
Solution for decarbonizing cement industry
According to WWF ‘’A blueprint for a climate friendly cement industry’’ report, solutions that can help reduce CO2 emissions of cement industry are: (Source: awassets.panda.org)
- Improving the thermal efficiency of kilns.
- Increasing the share of biomass.
- Improve the electrical efficiency of plants.
- Developing Carbon Capture and Storage (CCS).
- Using cement more efficiently.
- Expanding the use of additives and substitutes to cement clinker.
According to the same report, every 10% decrease in the cement CO2 intensity by 2050 could save around 0.4 Gt CO2, and substantially contribute to slowing climate change.
According to Imperial College London report, main interventions to reduce CO2 emissions in the cement industry are:
- Using CCS technologies.
- Using biomass and municipal waste instead carbon intensive fuels.
- Substituting Clinker.
(Source: imperial.ac.uk)